Customer Relations
Quality Assurance Management Framework
Quality assurance in the Furukawa Company Group is based on the Quality Assurance Basic Policy and the Quality Assurance Action Guidelines. These set our basic policy as gaining the trust of our customers, providing products and services of quality that satisfy them, and contributing to society.
The organization that engages in comprehensive deliberations on important matters relevant to quality assurance in the Group is the Quality Assurance Committee, which was established at the headquarters of Furukawa Co., Ltd. In addition, the Quality Assurance Management Department has been established in the company's Technology Division to manage the Group's quality assurance framework and promote activities for quality assurance and product safety. Each organization takes steps for coordination while engaging the entire Group in our ongoing effort to provide manufacturing and service that will satisfy our customers and gain their trust.
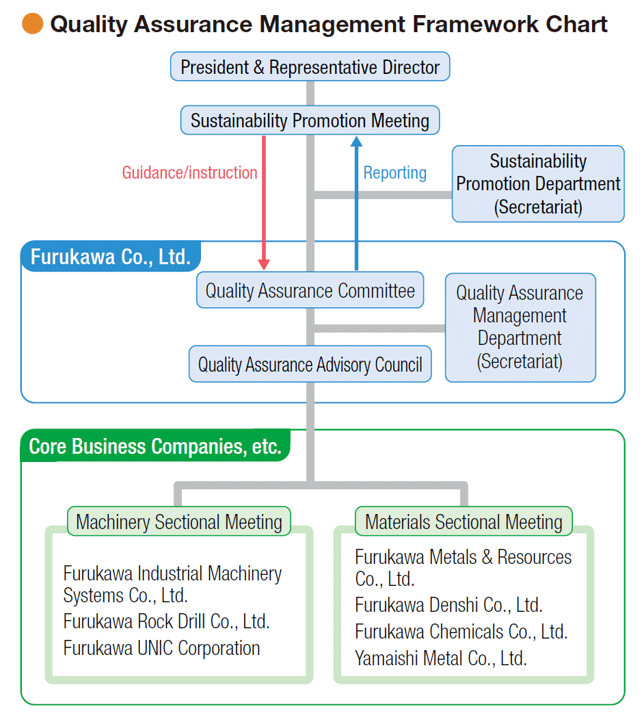
Quality Assurance Committee
Top managers from the production departments of the core operating companies consist of the Quality Assurance Committee.
This body has organized the Quality Assurance Advisory Council that brings together those responsible for quality assurance in the core operating companies and elsewhere. It also has organized sectional meetings with the Advisory Council members pursuing activities separately in the Machinery and Materials segments.
Seeking to achieve solutions to the key issues defined each fiscal year, we are sharing information on measures to analyze and reduce complaints at each site and seeking horizontal deployment of methods. We are also promoting compliance with laws and regulations relating to manufacturing, quality assurance, and product safety, and promoting the manufacture of products that customers can use in safety and with a sense of security. Based on the understanding that product safety is included in quality assurance, we are also continuously promoting risk assessment and other such activities to heighten product safety levels.
Machinery Sectional Meeting
In order for the Core Machinery-related Business Companies that consist of the Machinery Sectional Meeting to supply customers with satisfying products, we are comprehensively promoting information sharing among the sites together with monitoring of key processes aimed at reducing the number of complaints. Change point control is positioned as a key item for verification as a preventive measure. We are also strengthening the active monitoring of design review, initial flow management, risk assessment during development, and other such activities. Onsite, we periodically implement quality patrols by workplace and theme.
Since quality is created by each department, all Group officers and employees, and cooperating suppliers, and provided to customers, the ideal is to assure the results of a consecutive flow of processes that are completed at each area of assignment. To this end, we are promoting quality education to bring each process closer to the completion in the assignments and to realize quality improvement from the bottom up. As to the Small-group manufacturing improvement activities that are conducted periodically at every site, we have also been upgrading the activity content as an opportunity to think about how to handle one's independent processes.
Recent years have brought dizzying advances in such digital information environments and tools as digital transformation (DX), extended reality (XR), and so on. The Machinery segment core operating companies have these in operation or trial use, for example in the use of work navigation systems, the application of sensing and information analysis software, and so on. While carefully studying the validity of these systems, we will continue promoting their introduction to raise production efficiency, improve quality, and help improve the environment.
Materials Sectional Meeting
Participants in the Materials Sectional Meeting are the core operating companies that provide materials widely used in electronic and other such equipment. In October 2021, the Yamaishi Metal Co., Ltd. became a company subsidiary and was included in the Materials Sectional Meeting. Based on our customer-focused approach, the meeting has targeted zero complaints and is engaged in improving its quality assurance system, extending to the goods procured overseas.
In the Materials segment core operating companies, risk assessment involves the use of safety data sheets and other means to provide risk information. The release of defective products is also considered a major risk, and we have promoted its prevention by implementing failure mode and effects analysis (FMEA*1), which focuses on change point control, to achieve highly reliable design and automation of inspection. At this sectional meeting, such information is shared and, together with activities to upgrade the skills of each company, the reduction of defects within processes is also being addressed.
The target of zero complaints was declared again in fiscal 2023, with continuous implementation of highly reliable design, prevention of defective product releases, and improvement of the quality assurance framework, extending to goods procured overseas. Every company in the Materials Sectional Meeting will be engaging in activities to further upgrade their skills.
- *1FMEA: Abbreviation for Failure Mode and Effects Analysis. A systematic analysis method that predicts the causes of quality problems and prevents them at the design and process planning stage.
ISO 9001 Certification Acquisition Status
Company Name | Acquisition Date | Certification Organization |
---|---|---|
Furukawa UNIC Corporation | June 6, 1997 | Japan Quality Assurance Organization (JQA) |
Furukawa Rock Drill Co., Ltd. | October 17, 1997 | TÜV Rheinland Japan Ltd. |
Furukawa Industrial Machinery Systems Co., Ltd. | June 22, 1999 | Nippon Kaiji Kyokai (ClassNK) |
Furukawa Denshi Co., Ltd. | December 4, 1998 | Japan Quality Assurance Organization (JQA) |
Yamaishi Metal Co., Ltd. | November 28, 2000 | Bureau Veritas Japan Co., Ltd. |
Furukawa Chemicals Co., Ltd. | July 24, 2003 | JIC Quality Assurance Ltd. (JICQA) |
Tsukuba Site, Technology Division, Furukawa Co., Ltd. (Material Research & Development Dept. / Advanced Technology Dept.) |
January 14, 2004 | JSA Solutions Co., Ltd. |
FURUKAWA UNIC (THAILAND) CO., LTD. | May 14, 2009 | Perry Johnson Registrars, Inc. |
Taian Furukawa UNIC Crane Co., Ltd. | November 8, 2010 | Shanghai Audit Centre of Quality |
FD COIL PHILIPPINES, INC. | March 24, 2021 | United Registrar of systems Ltd. |